Reasons and solutions for the breakage of the vibrating screen
May.13,2019
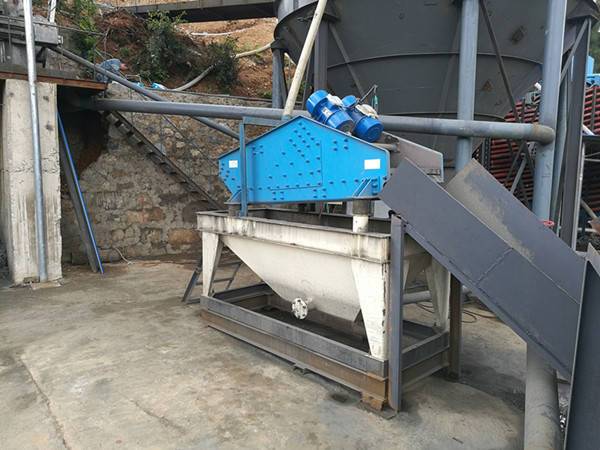
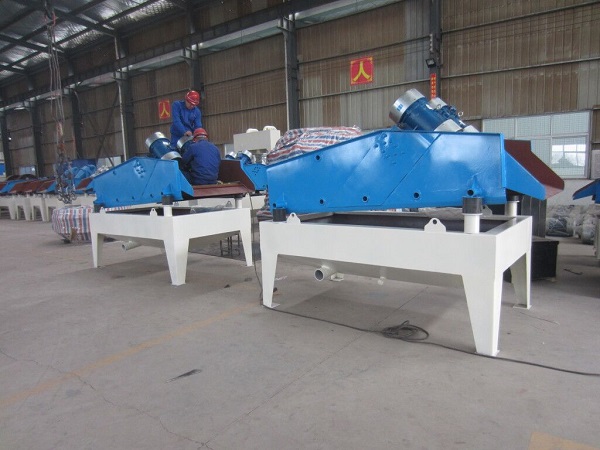
The cause of the failure: the screen machine caused by the side plate of the screen box is not thick enough or the beam diameter is too small, which can not adapt to the harsh production environment and cracking.
Solution: Find the main force point, strengthen the ribs near the exciter, and install the ribs near the four support feet to strengthen the strength of the screen side panels.
The cause of the failure: the yaw of the vibrating screen causes the sieve plate to crack.
Solution: The unbalance of the support feet, the failure of the shaker or the inconsistent force will cause the screen to crack. Check the blanking situation and periodically measure the height of the support foot damping spring to ensure the balance of the support feet. Regularly screen each part to ensure that the equipment is not faulty, and when lubricating, each of the exciter bearings is quantitatively lubricated to ensure that the resistance of the vibrator in each exciter is generally the same, ensuring that the vibration trajectory is normal.
Cause of failure: The vibrating screen generates resonance, causing cracking failure.
Solution: Improve the vibrating screen surface support ribs, increase the number of intermediate support ribs in the screen, and each one is consistent with the middle one. It has the function of installing fixing bolts, and is pressed by multiple pressure plates to ensure reliable fixing of the screen. , unable to reach resonance.
Cause of failure: Reconstruction measures for equipment failure caused by production load.
Solution: The material is very viscous and difficult to screen, resulting in the proper size of the upper layer material, and the actual load exceeds the rated load of the equipment, causing failure. The inclination angle of the vibrating screen can be appropriately increased to increase the sliding speed under the screen surface and reduce the thickness.