Requirements for high quality fracturing sand oil frac sand
April.16,2019
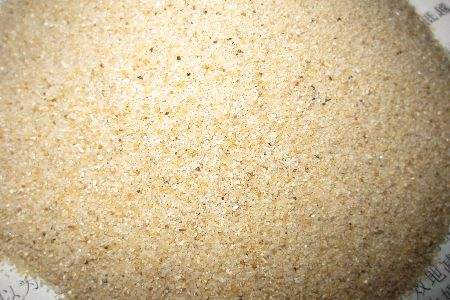
Frac Sand
What is frac sand?
Frac sand (fracturing sand) is high-purity quartz sand with superior pressure resistance and high roundness. This substance is artificially crushed and used mainly in the petroleum industry. Especially in the application of hydraulic fracturing, the high-pressure water pump is used to inject the fracturing fluid into the oil and gas reservoir, and the reservoir is crushed to obtain oil and gas resources. Fracturing sand is an indispensable substance. Most of the silica sand comes from high-purity quartz sandstone, but there are also some substitutes for quartz sand, such as ceramsite and metal particles. When fracturing, the fracturing of wells generally uses fracturing sand with a particle size of 400-800 um. Natural quartz sand (600/300μm, 425/212μm).
Requirements of silica sand on size, grade
The oil frac sand is filled with the high pressure solution into the formation and filled in the fracture of the rock stratum, so as to support the fracture without closing due to stress release, thereby maintaining high conductivity, smoothing oil and gas, and increasing production. Performance requirements of petroleum fracturing sand:
1. The proppant should have sufficient compressive strength and anti-wear ability, can withstand the strong pressure and friction during injection, and effectively support artificial cracks.
2. The relative density of proppant particles is low, which is easy to pump into the well. When fracturing, the fracturing of water wells generally uses fracturing sand with a particle size of 400-800 um. Natural quartz sand of 600/300μm, 425/212μm.
3. The proppant particles do not chemically react with the fracturing fluid and the reservoir fluid under the condition of temperature of 200 °C. The maximum allowable value of acid solubility should be less than 7%.
Frac sand processing/washing equipment
Equipment for washing fracturing sand for oil field, including interconnected hoist and sand tank, the discharge port of the sand tank is connected with a spiral sand washing machine, and the discharge chute and cylinder washing sand screening of the spiral sand washing machine The machine is connected, the trommel screen is connected with the dewatering spiral sand washing machine; the dewatering spiral sand washing machine is connected with the dewatering equipment, and the main body rotation axis and the level of the dewatering equipment are 30-35 degrees.
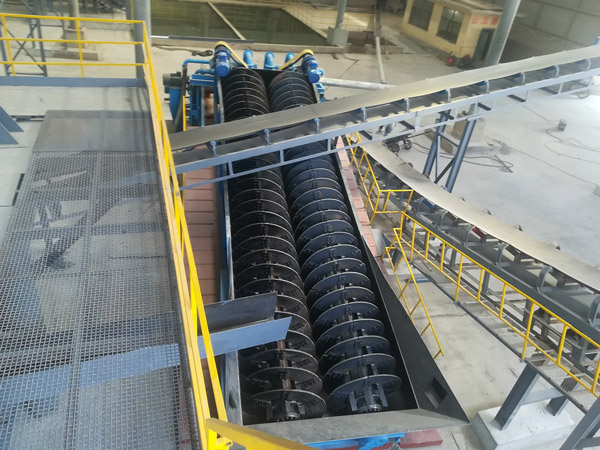
screw washer
At present, the commonly used frac sands mainly include quartz sand, aluminum vanadium ceramsite sand and resin-coated composite particles. Due to the low cost of quartz sand and the low density and easy pumping, it is widely used. However, quartz sand has low strength and poor sphericity, which reduces the ability of crack conductivity and is not suitable for deep wells with high closing pressure.
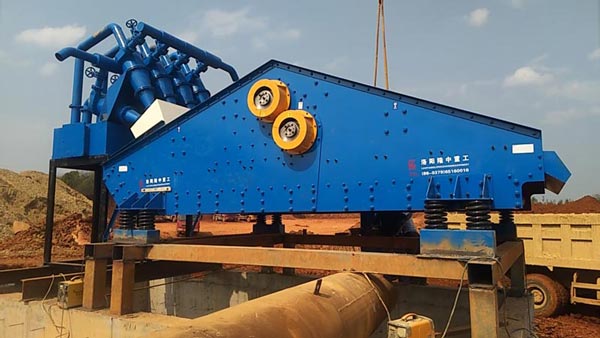
dewatering screen
The composite particles coated with quartz sand have improved sphericity, strong corrosion resistance, and good conductivity. However, the product retention period is short and the cost is too high. It is not easy to promote the cost first, and the aluminum bauxite is used. The ceramsite proppant of the ceramsite process has high density, good sphericity, corrosion resistance, high-temperature resistance, and high-pressure resistance, and the cost can be well controlled, so it is more and more widely used by oil and gas fields.
The practice has proved that oil wells fractured with ceramsite petroleum proppant can increase production by 30-50% and extend the service life of oil and gas wells. It is a key material for oil and gas low-permeability oil and gas wells mining and construction, which can not only increase oil and gas production. And it can extend the service life of oil and gas wells. We can produce high-quality frac sand processing and washing equipment.