Extracting gold copper iron aluminum metals from domestic waste slag
December.28,2023
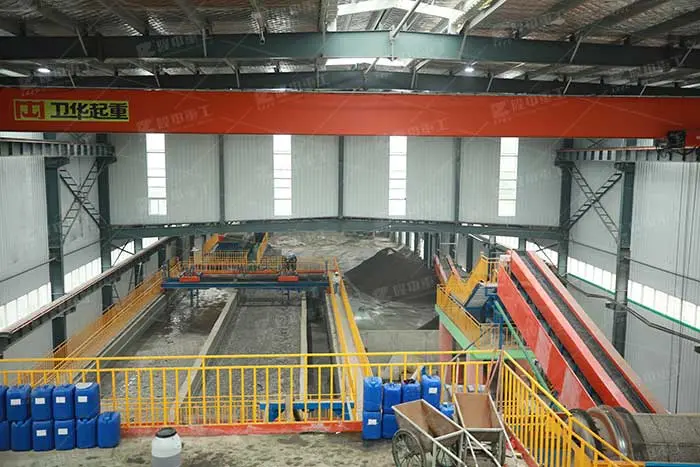
Waste incineration slag refers to the solid waste generated during the waste incineration process, including slag and bottom slag. Slag refers to the solid waste produced during the incineration process, and bottom slag refers to the ash and unburned materials at the bottom of the furnace. These wastes contain a certain amount of precious metals, such as gold, silver, copper, platinum, etc. Therefore, higher economic benefits can be obtained by refining waste incineration slag.
Steps to extract metal from waste incineration slag
Simplified process flow diagram
1. Pretreatment of waste incineration slag: crush and screen the waste incineration slag to make it suitable for subsequent treatment.
2. Separation and extraction of metals: Separate metals from waste incineration slag through magnetic separation, flotation or gravity selection.
3. Refining and purifying metals: Refining and purifying the separated metals to obtain high-purity metal materials.
4. Waste residue treatment: Treat the separated waste residue to make it meet environmental protection requirements.
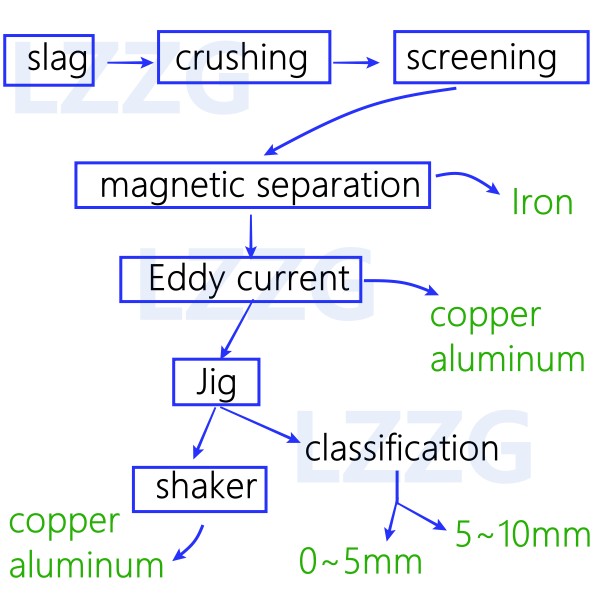
Equipment used for slag sorting
The equipment used in the slag production line includes: screening, crushing, magnetic separation, gravity selection jig, gravity selection shaker, dehydration screen, automatic filter press and conveyor. The following is a systematic analysis of the equipment:
1. Drum screen
The slag is shoveled out from the slag warehouse by a forklift, the material is loaded into the hopper, and then sent to the drum for screening using a conveyor belt to separate large and small materials.
2. Slag crusher
The slag crusher crushes the processed materials to ensure uniform particle size of the slag discharged. Therefore, it is the best equipment choice for the slag crushing production line.
3. Magnetic separator
Magnetic separation is used to select magnetic materials, and then non-magnetic metal materials and raw materials are manually sorted.
4. Sawtooth wave jig
The processed slag is separated again on the jig machine, and the hole diameter of the jig net is about 5mm. Water needs to be added during the jigging process. The water consumption in the jigging process is 2.0m³ per ton of slag.
5. Ore dressing shaker
The non-magnetic separation enters the shaking table for treatment. Under the action of the shaking table groove and hydraulic power, non-ferrous metal particles, such as copper, aluminum, gold, silver, stainless steel, etc., are separated and collected.
6. Dewatering screen
After the slag-water mixture is dehydrated by the dehydration screen equipment, it reaches the slag-water separation state. The slag is driven into the feed port of the dehydration screen through the slag pump or through the height difference. The dehydration screen passes through two vibrating motors in a straight line from the feed port to the discharge port. Movement, the slag on the screen is automatically discharged, the water is discharged from under the screen, and the water under the screen enters the settling tank and is returned to water for use after settling.
7. Filter press
The moisture content of the finished slag is about 30%, ensuring no water leakage during transportation. The moisture content of the residue after filtration by the frame filter press is generally 30 to 35%, and no water will appear on the residue after filtration. Author: Longzhong Heavy Industry Technology https://www.bilibili.com/read/cv27325167/?jump_opus=1 Source: bilibili